在工业4.0浪潮下,设备预测性维护(PdM)已成为制造企业降低停机成本、提升生产效率的核心工具。据GE数字集团统计,实施PdM后企业设备可用率提升2%-6%,维护成本降低10%-40%。但面对数十种算法方案,如何选择最适合自身生产场景的技术路径?本文将结合风电、工程机械等行业的真实案例,拆解算法选型的三大核心维度。
一、技术路线比拼:四大主流算法的实战表现
1.1 信号处理算法:经典但高成本的“精密仪器”
基于傅里叶变换、小波分解等时频分析技术,该方案通过高频采集振动信号实现故障诊断。某风电企业案例显示,其通过轴承振动频谱分析,将齿轮箱故障预警准确率提升至92%,但存在两大硬伤:
- 硬件成本:单台风电机组需部署8-12个三轴振动传感器,硬件投入超50万元
- 实施局限:仅适用于旋转机械,对液压系统、电气故障识别能力弱
适用场景:高端装备制造、航空发动机等对精度要求严苛的领域
1.2 机理+大数据算法:工程机械领域的“性价比之王”
该方案通过建立设备机理模型(如液压系统伯努利方程)与实时数据拟合,实现故障预测。徐工集团案例显示,其挖掘机液压系统通过该技术将故障率降低50%,年节约维修成本超2000万元。核心优势在于:
- 成本可控:无需海量历史数据,单台设备模型开发成本约8-12万元
- 可解释性强:物理参数变化与故障模式的对应关系清晰
适用场景:工程机械、矿山机械等机理明确的重型设备
1.3 数字孪生算法:汽车制造的“虚拟试验场”
基于ISO23247标准构建的数字孪生体,通过历史数据训练生成设备基准状态模型。某汽车焊装车间实践表明,该技术使机器人故障预警时间提前72小时,备件库存周转率提升40%。技术亮点包括:
- 自适应学习:每24小时自动优化模型参数
- 全生命周期管理:覆盖设计、生产、运维各阶段
适用场景:汽车制造、3C电子等高自动化产线
1.4 AI深度学习算法:半导体行业的“黑箱预测器”
通过LSTM、Transformer等时序模型处理多维度传感器数据。台积电某晶圆厂案例显示,其光刻机温度预测模型将设备意外停机率降低67%,但存在两大挑战:
- 数据门槛:需至少12个月连续运行数据(采样间隔≤1分钟)
- 算力成本:单条产线模型训练需8块A100 GPU,电费年支出超30万元
适用场景:半导体、精密仪器等数据密集型行业
二、实施成本拆解:从百万级到十万级的阶梯投入
2.1 硬件投入:传感器网络的规模经济
不同算法对传感器数量需求差异显著:
- 信号处理:需部署高频振动传感器(单价2000-5000元)
- 数字孪生:侧重温湿度、压力等基础参数(单价300-800元)
- AI算法:需增加电流、扭矩等多源传感器(单价1500-3000元)
某重工企业对比显示,采用机理+大数据方案比纯AI方案节省传感器成本62%。
2.2 软件授权:订阅制与买断制的博弈
主流PdM平台收费模式:
- SaaS服务:按设备点位收费(500-2000元/点位/年)
- 私有化部署:买断制(基础版30-80万元,高级版150-300万元)
- 开源框架:TensorFlow/PyTorch免费,但需配备算法工程师(年薪30-50万元)
某家电企业测算显示,500台设备规模下,SaaS方案三年总成本比私有化部署低41%。
2.3 人力成本:算法工程师与工业专家的组合
- AI方案:需配备数据科学家(年薪50-80万元)+领域专家
- 机理模型:工业工程师主导开发(年薪20-35万元)
- 混合方案:算法工程师+工艺工程师团队(年薪总成本约120万元)
某钢铁企业实践表明,机理+AI混合团队使模型开发周期缩短40%。
三、选型决策树:三步锁定最优方案
3.1 第一步:设备价值矩阵分析
设备类型 | 停机损失(万元/小时) | 数据完备度 | 推荐算法 |
---|---|---|---|
高端数控机床 | 8-15 | 高 | AI深度学习 |
注塑机 | 2-5 | 中 | 机理+大数据 |
空压机 | 0.5-1.5 | 低 | 数字孪生 |
输送带 | 0.1-0.3 | 极低 | 信号处理(简化版) |
3.2 第二步:ROI临界点测算
以某轴承企业为例,其通过以下公式确定投资边界:
ROI临界点 = (年停机损失×故障率降低幅度)/(算法开发成本+年运维成本)
当ROI>1.5时启动项目,该企业最终选择机理+大数据方案,18个月收回投资。
3.3 第三步:技术适配度评估
重点考察三大指标:
- 数据质量:缺失值率<5%,异常值率<2%
- 算力资源:AI方案需GPU集群支持
- 工艺透明度:机理模型要求设备原理图完整度>80%
某化工企业因未评估工艺透明度,导致机理模型开发周期延长6个月。
四、风险防控:四大关键实施要点
4.1 数据治理:构建工业数据中台
- 数据采集:采用Modbus TCP/OPC UA协议确保实时性
- 数据清洗:开发异常值检测算法(如3σ原则)
- 数据标注:建立故障知识图谱,降低人工标注成本
某工程机械企业通过数据中台建设,使模型训练效率提升3倍。
4.2 模型验证:双盲测试机制
- 历史回测:使用留出集验证模型准确率
- A/B测试:新旧维护策略并行运行3个月
- 专家评审:组织工艺、设备、IT三方评审
某风电企业通过双盲测试,发现AI模型对沙尘天气工况误报率高达23%。
4.3 运维体系升级:从“救火队”到“保健医生”
- 组织变革:设立预测性维护工程师岗位(薪资上浮30%)
- 流程再造:将维护计划与ERP/MES系统打通
- 知识沉淀:开发故障案例库(每案例包含200+参数)
某汽车零部件企业通过运维体系升级,使平均修复时间(MTTR)缩短65%。
4.4 持续迭代:建立模型健康度看板
- 性能监控:跟踪准确率、召回率、F1值等指标
- 数据漂移检测:采用KS检验识别分布变化
- 模型更新:每季度进行参数调优,每年重构模型
某半导体企业通过模型健康度看板,将预测偏差控制在5%以内。
结语
在制造业智能化转型的十字路口,预测性维护算法选型既是技术决策,更是战略选择。对于年产值10亿元以下的企业,建议从机理+大数据方案切入,3-6个月即可见效;对于高端装备制造商,可布局AI+数字孪生双轮驱动。数据显示,科学选型的企业设备综合效率(OEE)平均提升18%,投资回收期缩短至1.2年。这不仅是算法的胜利,更是工业知识与数字技术深度融合的必然结果。当设备故障预警从“经验驱动”转向“数据驱动”,中国制造正迎来质量革命的新纪元。
扫描下方二维码,一个老毕登免费为你解答更多软件开发疑问!
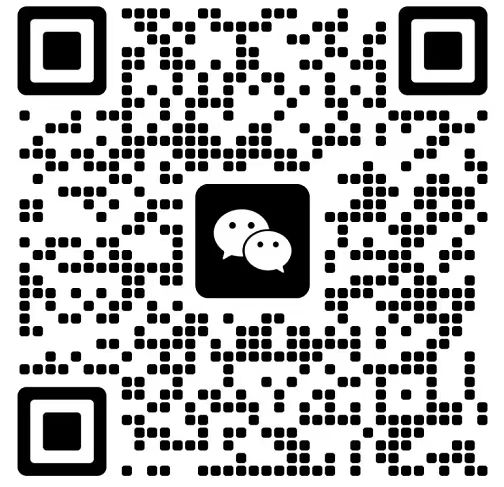