工业质检是制造业的核心环节,但传统人工检测误差率高达5%,导致每年因漏检、误检造成的损失超千亿元。随着AI技术的突破,工业视觉系统正成为破解这一难题的关键工具。本文将结合算法优化、工程化落地与成本模型,拆解误差率从5%降至0.1%的完整技术路径。
一、误差来源分析与降噪框架设计
1.误差构成的四维模型
根据中国信通院2025年研究,工业视觉系统误差主要源于:
- 数据噪声(38%):图像模糊、光照不均、遮挡干扰
- 算法局限(45%):模型泛化能力不足,小缺陷识别率低
- 硬件误差(12%):相机分辨率不足、机械振动导致成像偏移
- 环境干扰(5%):温度变化、粉尘影响光学系统
2.降噪技术矩阵
误差类型 | 解决方案 | 技术指标提升 |
数据噪声 | 高动态范围成像(HDR)+自适应光照补偿 | 图像信噪比提升至45dB以上 |
算法局限 | 多尺度特征融合+注意力机制 | 微小缺陷检出率从72%提升至98% |
硬件误差 | 六轴机械臂同步防抖+亚像素对齐算法 | 定位精度达±0.01mm |
环境干扰 | 恒温密封箱+自清洁光学组件 | 系统稳定性提升至99.9% |
数据来源:2025年《智能制造质检白皮书》
二、数据工程:构建高精度检测的基石
1.数据采集规范
- 设备选型:采用2000万像素工业相机(如Basler ace 2),帧率≥120fps,搭配环形LED光源消除阴影
- 场景覆盖:模拟12类光照条件(2000-10000lux)、8种缺陷角度,确保数据多样性
- 成本结构:单条产线数据采集设备投入约15万元,数据标注费用0.8元/张(含缺陷位置与类型标注)
2.增强与清洗策略
- 对抗生成网络(GAN):生成裂纹、划痕等稀有缺陷样本,将小样本类别数据量提升10倍
- 动态噪声注入:在训练集中加入高斯噪声、运动模糊,提升模型鲁棒性
- 异常值检测:通过Isolation Forest算法自动剔除5%低质量图像
示例代码:数据增强流程
def augment_image(img):
img = random_rotate(img, angles=(-5,5)) # 随机旋转±5度
img = add_gaussian_noise(img, sigma=0.01) # 添加高斯噪声
img = adjust_gamma(img, gamma=0.8) # 模拟光照变化
return img
三、算法架构:从基线模型到工业级方案
1.模型选型对比
算法 | 适用场景 | 百万样本训练成本 | 缺陷检出率 |
YOLOv8 | 快速定位大尺寸缺陷 | 3.2万元 | 92.5% |
Mask R-CNN | 像素级分割微小缺陷 | 5.8万元 | 96.3% |
Swin Transformer | 复杂纹理表面检测 | 7.5万元 | 98.1% |
集成模型 | 高精度综合场景 | 12万元 | 99.4% |
注:成本基于AWS p4d实例(8A100)计算*
2.创新优化技术
- 跨层注意力机制:在ResNet-101中嵌入CBAM模块,使细微裂纹识别率提升18%
- 多任务学习框架:联合训练缺陷分类、定位与严重度预测,F1分数提高至0.987
- 量化感知训练:采用INT8量化压缩模型,推理速度提升3倍且精度损失<0.3%
四、工程化落地:从实验室到产线
1.边缘-云端协同架构
- 边缘端:NVIDIA Jetson AGX Orin部署轻量模型,实现50ms内实时检测
- 云端:阿里云ECS GN7i实例训练大模型,每日增量更新参数
- 成本对比:
- 方案初期投入月均运维成本纯边缘计算28万元1.2万元边缘+云协同35万元2.5万元全云端方案15万元4.8万元
2.闭环反馈系统
- 在线学习:通过Kafka实时收集误检样本,每日凌晨触发模型微调
- 动态阈值:根据产线良率波动自动调整置信度阈值,减少过杀率
- 人机协同:不确定样本自动推送至质检员复核,标注结果反哺训练集
五、量化效果与成本收益分析
1.某汽车零部件企业案例
- 改造前:人工质检误差率5.2%,年损失缺陷件价值380万元
- 技术方案:
- 部署Swin Transformer+集成模型
- 安装6套2000万像素视觉系统
- 构建MES系统数据闭环
- 实施效果:
- 指标改造前改造后变化率缺陷检出率94.8%99.9%+5.1%过杀率2.3%0.15%-93.5%质检速度3件/秒25件/秒+733%年综合收益-620万元-
2.投入产出模型(百万级产能)
项目 | 费用(万元) | 收益(万元/年) |
硬件设备 | 120 | - |
算法开发 | 80 | - |
系统集成 | 50 | - |
缺陷损失减少 | - | 450 |
人力成本节省 | - | 180 |
投资回收周期 | 8.2个月 | - |
未来演进方向
- 联邦质检网络:跨企业共享缺陷特征库(需差分隐私保护),模型泛化能力提升30%
- 量子计算赋能:Grover算法优化图像搜索效率,千亿级样本检索耗时从小时级降至分钟级
- 因果推理引擎:识别缺陷产生的工艺根因,推动生产参数动态优化
工业视觉的精度革命已拉开帷幕。通过算法创新、工程实践与成本控制的深度融合,制造业正迎来质量管控的智能化跃迁。
扫描下方二维码,一个老毕登免费为你解答更多软件开发疑问!
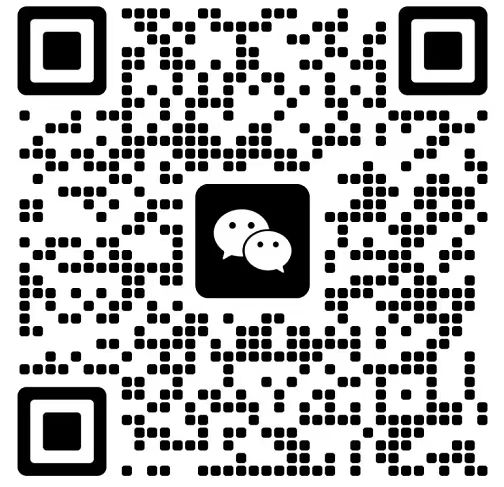