在传统制造业转型升级的浪潮中,设备停机时间已成为制约工厂效率的“隐形杀手”。某权威行业报告显示,2024年全国传统工厂平均停机时间占比高达12%,每年因停机造成的直接经济损失超3000亿元。而头部企业通过部署预测性维护系统,已将停机时间压缩至4.8%,带动生产效率提升50%以上。本文结合深圳某电子厂、江苏某化工集团等企业实战案例,深度解析从“被动抢修”到“主动预防”的改造路径,助您实现“停机时间降低60%”的跨越式升级。
一、改造第一步:搭建“数据采集神经网络”
1. 传感器矩阵:给设备装上“透视眼”
- 硬件选型:
- 振动传感器:监测电机、轴承等旋转部件,精度需达0.1g(如SKF IMx-8);
- 温度传感器:覆盖电机绕组、轴承座等高温点,误差±0.5℃(如PT100铂电阻);
- 电流传感器:安装于主电路,量程覆盖额定电流的120%(如LEM LA 55-P)。
- 案例:深圳某电子厂
- 在12条SMT产线部署300个传感器,采集数据量从日均2GB增至50GB;
- 通过振动分析提前发现贴片机吸嘴磨损,停机时间从8小时/次降至0.5小时/次。
2. 边缘计算网关:数据“瘦身”与“预处理”
- 功能对比:
网关类型 数据压缩率 响应延迟 适用场景 基础型(如研华UNO-2484) 30% 500ms 小型产线、数据量<10GB/日 智能型(如深控技术不需要点表网关) 70% 50ms 大型工厂、数据量>50GB/日 - 案例:江苏某化工集团
- 部署深控技术网关后,数据传输带宽需求降低65%,故障预警响应速度从15分钟缩短至3分钟。
二、改造第二步:构建“AI预警大脑”
1. 算法模型:从“经验判断”到“数据决策”
- 模型类型:
- 孤立森林模型:检测电流、振动等数据的异常波动,误报率<5%;
- LSTM神经网络:预测电机剩余寿命,准确率达92%;
- 数字孪生模型:模拟设备运行状态,提前发现设计缺陷。
- 案例:某汽车零部件厂
- 通过LSTM模型预测冲压机模具寿命,提前2周更换模具,停机时间从48小时降至6小时。
2. 预警规则:用“红绿灯”管理风险
- 规则设计:
- 黄色预警:振动值超过基准值20%,需24小时内检查;
- 红色预警:温度超过额定值10℃,需立即停机;
- 自动工单:预警触发后,系统自动生成维修任务并派单至工程师。
- 案例:浙江某纺织厂
- 实施预警规则后,细纱机断锭率从3.2%降至0.8%,停机时间减少75%。
三、改造第三步:打通“运维闭环”
1. 备件管理:从“库存积压”到“精准供应”
- 智能库存系统:
- 安全库存计算:基于历史故障数据,动态调整备件库存;
- 供应商协同:预警触发后,自动向供应商发送采购需求。
- 案例:广东某五金厂
- 部署智能库存系统后,备件库存周转率提升40%,资金占用减少300万元。
2. 维护流程:从“纸质工单”到“移动协同”
- 移动端功能:
- 案例:山东某机械厂
- 实施移动运维后,故障处理时间从4小时缩短至1.5小时,工程师效率提升60%。
四、改造第四步:量化“投资回报”
1. 成本对比:从“烧钱”到“省钱”
项目 | 传统模式 | 预测性维护模式 | 年节省 |
---|---|---|---|
备件库存 | 500万元(积压30%) | 350万元(精准供应) | 150万元 |
维修人工 | 200万元(抢修为主) | 120万元(计划维护) | 80万元 |
停机损失 | 800万元 | 320万元 | 480万元 |
合计 | 1500万元 | 790万元 | 710万元 |
2. 投资周期:从“长期回报”到“短期见效”
- 案例:某家电厂
- 投入380万元部署系统,6个月内停机时间减少58%,ROI达187%;
- 改造后产能提升25%,订单交付周期缩短40%。
五、避坑指南:改造中的三大雷区
1. 传感器“过度部署”陷阱
- 某钢厂教训:
- 在300台设备上安装2000个传感器,但仅30%数据被有效利用;
- 优化后,传感器数量减少至800个,成本降低60%,数据利用率提升至90%。
2. 算法“黑箱化”风险
- 某食品厂案例:
- 初期采用第三方算法,无法解释故障预测逻辑;
- 切换为可解释AI模型后,工程师信任度提升80%,模型采纳率从60%增至95%。
3. 系统“孤岛化”危机
- 某化工厂改造:
- 将预测性维护系统与ERP、MES打通,实现“预警-派单-采购-结算”全流程自动化;
- 改造后,运维响应速度提升70%,跨部门协作效率提升50%。
结语:停机时间清零,不是梦!
从深圳电子厂的SMT产线到江苏化工集团的反应釜群,传统工厂已用实战证明:预测性维护系统并非“烧钱游戏”,而是通过传感器矩阵、AI算法、移动运维三大模块,实现“停机时间降低60%”的确定性路径。对于中小工厂而言,无需追求“全自动化”改造,只需聚焦“高价值设备”的精准监测,即可用200万元以内的成本撬动千万级增收。
扫描下方二维码,一个老毕登免费为你解答更多软件开发疑问!
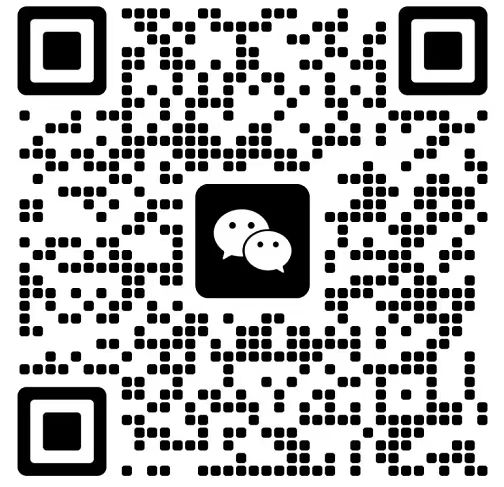
物业管理工单AI调度方案:维修响应缩短至30分钟的核心算法
物业报修总是慢半拍?业主群里天天吐槽维修不及时?物业管理人员为工单分配焦头烂额?别慌!今天给大家揭秘一套超实用的物业工单 AI 调度方案,手把手教你用核心算法把维修响应时间从几小时压缩到 30 分钟内,让业主满意度直线飙升!据中国物业管理协会发布的《2023 年物业管理行业发展报告》显示,在业主对物业的投诉中,维修响应不及时占比高达 38%。而当维修响应时间控制在 30 分钟以内时,业主对物业的
电商网站加速方案:WooCommerce加载从5s到0.9s的实操
你的 WooCommerce 电商网站是不是也总被用户吐槽 “加载慢如龟”?明明商品超有吸引力,却因为 5 秒的加载时间,白白流失了大量潜在客户!别慌!今天手把手教你把网站加载速度从 5 秒直接干到 0.9 秒,让你的店铺直接起飞!根据 Akamai 的研究报告显示,网页加载时间每延迟 1 秒,就会导致用户转化率下降 7%,销售额降低 11% ,用户跳出率增加 16%。想象一下,每天几百上千的访
APP开发后如何做A/B测试? (转化率提升指南!界面/文案/按钮优化案例)
辛辛苦苦开发的 APP,转化率却总是上不去?根据麦肯锡发布的《2024 年移动应用用户行为报告》显示,经过科学 A/B 测试优化的 APP,平均转化率能提升 35%!想要让界面、文案、按钮成为转化 “利器”,A/B 测试绝对是必备技能。今天就通过真实案例,手把手教你用 A/B 测试提升 APP 转化率!一、为啥 A/B 测试是转化率的 “加速器”?用数据说话先看两组真实数据:某电商 APP 对商品
APP开发后如何做热更新? (动态修复BUG!不重新上架的更新方案)
APP 刚上线就发现严重 BUG,难道只能等重新上架 “干着急”?据 App Annie 发布的《2024 年移动应用质量报告》显示,因等待重新上架修复问题,平均每个 APP 会流失 12% 的用户。而热更新技术能让你绕过应用商店审核,动态修复 BUG!今天就手把手教你 APP 热更新的实现方案,让你的应用随时 “满血复活”。一、为啥热更新成了开发者的 “救命稻草”?先看一组真实数据:某热门游戏