在制造业专家年均差旅成本突破120万元/人的行业背景下,某装备制造企业通过部署AR远程协助系统,将专家差旅频次从年均150次降至30次,年度差旅费用直降82万元,设备停机时间缩短68%。这一数据背后,是空间计算技术对传统售后模式的颠覆性改造,其落地路径、成本效益与用户体验正引发行业震动。
一、行业困局:专家“飞人”背后的成本黑洞
据中国机械工业联合会《2024装备制造业服务化转型报告》显示,全国装备制造企业年均设备故障导致的停机损失超2000亿元,其中70%的故障可通过远程协助解决,但传统方式下专家到场率不足40%。某风电企业运维总监无奈表示:“一台风机故障,专家从北京飞到西北戈壁,光差旅费就要2万元,还耽误3天生产。”
传统售后模式痛点:
- 响应滞后:专家平均到场时间超48小时,设备停机损失每日超50万元;
- 成本高昂:单次差旅(机票+住宿+补贴)平均成本1.8万元,年均支出超百万;
- 资源错配:80%的故障可通过远程指导解决,但因技术限制被迫现场处理。
二、技术突破:AR眼镜构建“数字分身”服务网络
该企业联合技术团队开发的AR远程协助系统,通过“三维标注+实时协作+智能诊断”三位一体方案,实现从“专家飞人”到“数字协同”的跨越:
技术架构拆解:
- 硬件层:
- 工业级AR眼镜(RealWear HMT-1Z1):支持12小时续航、IP66防护等级,单价1.2万元/台;
- 5G工业路由器:保障低延迟传输(端到端时延<50ms),设备成本0.8万元/台;
- 软件层:
- 三维标注系统:支持在设备表面叠加虚拟箭头、文字说明,准确率达98%;
- 语音转文本:自动生成维修日志,减少30%的记录工作量;
- 多方协作:支持现场人员、远程专家、供应商三方同屏协作;
成本对比:
- 传统方案:
- 专家年薪:60万元(含奖金)
- 年均差旅费:120万元(含机票、住宿、补贴)
- 单次故障处理成本:约2.3万元(差旅+停机损失)
- AR方案:
- 硬件投入:HoloLens 2眼镜(单价3.5万元)×10台=35万元
- 软件成本:定制化开发费用50万元(含三年维护)
- 运维成本:系统升级+维护费约8万元/年
- 年度总成本:AR方案(硬件35万+软件授权费15万/年=50万元(首年投入,后续年运维约5万元
- 年度总成本:AR方案(85万元) vs 传统方案(180万元+差旅费80万元)= AR方案节省75%
- 长期成本:AR系统维护费约8万元/年,差旅成本随使用量下降可节省超80万元/年。
二、技术突破:AR如何让专家“分身有术”?
该企业联合技术团队开发的AR远程协助系统,通过“空间标注+多端协同+AI辅助”三重技术,实现从“物理到场”到“数字在场”的跨越:
技术架构拆解:
- 硬件层:
- 选用Microsoft HoloLens 2头显(单价3.5万元)×10台 + 5G工业路由器(单价8000元)×5台 = 39万元(首年投入);
- 支持手势交互、空间锚定、热力图可视化,精度达毫米级;
- 软件层:
- 3D模型库:预载2000+设备模型,支持实时渲染;
- AI辅助诊断:接入设备历史数据,自动生成故障概率图谱;
- 多端协同:支持专家、现场工程师、客户三方实时标注与语音沟通;
- 安全层:
- 军工级加密传输,确保设备数据不出厂区;
- 操作日志全程留痕,符合ISO 27001认证;
成本对比:
- 传统方案:
- 专家差旅:机票(年均150次×2000元)+ 住宿(150次×500元)+ 误工成本(150次×2000元/天) = 年均82.5万元;
- 设备停机损失:日均50万元×停机天数(年均45天)= 2250万元;
- AR方案:
- 硬件投入:首年39万元 + 年维护费5万元;
- 软件订阅:10万元/年(含模型更新);
- 年度总成本:AR方案(54万元/年) vs 传统方案(差旅80万+人力成本20万=100万/年),节省46%;
- 隐性收益:设备停机损失减少(按单日50万元计算,年省超千万元);
三、用户体验:从“等专家”到“专家就在眼前”
技术落地后,生产现场的变革肉眼可见:
- 响应速度:
- 故障响应时间从72小时压缩至15分钟(远程指导启动自检程序);
- 某风电场齿轮箱故障,专家通过AR标注维修点,现场团队2小时完成修复(传统方式需3天);
- 知识沉淀:
- 所有AR维修记录自动生成知识库,新员工培训周期缩短40%;
- 某型号机床维修方案被复用127次,单次调用成本仅0.3元;
- 客户价值:
- 设备OEE(综合效率)从68%提升至82%;
- 客户主动续约率提高25%(因响应速度提升);
四、商业价值:从“成本中心”到“利润引擎”
- 运营效率:
- 单次维修平均耗时从72小时降至18小时(含远程准备时间);
- 某生产线因传动轴故障,通过AR远程指导,4小时内恢复生产(传统方式需3天);
- 成本优化:
- 差旅费用直降82万元/年;
- 设备停机损失减少约300万元/年(按每小时5万元损失计算);
- 生态扩展:
- 推出“AR维修即服务”(ARaaS),向中小客户按次收费(2000元/次),年创收超50万元;
- 与设备制造商合作,预装AR模块,分成收益超80万元/年;
五、技术落地:从“试点验证”到“全厂覆盖”
- 硬件部署:
- 在关键车间部署AR工作站(含头显+ 5G路由器),覆盖半径50米,单站成本8万元;
- 某车间部署2个工作站,覆盖全厂,总投入16万元;
- 流程再造:
- 故障上报→AR系统自动匹配专家→生成3D标注方案→现场执行→效果验证;
- 某次液压系统故障,系统推荐3套方案,维修时间缩短70%;
- 数据资产:
- 积累5000+故障案例,AI诊断准确率提升至92%;
- 反向优化产品设计,某型号机床改进后故障率下降65%;
六、行业变革:从“人力依赖”到“技术赋能”
- 竞争格局:
- 头部企业加速部署,某集团已覆盖80%的售后服务网点;
- 中小企业采用“订阅制”,按使用时长付费(150元/小时);
- 供应商响应:
- 核心零部件供应商接入AR系统,共享故障数据,备件配送准确率提升50%;
- 某轴承厂商通过AR指导客户安装,退货率下降80%;
- 标准制定:
- 行业联盟推出《AR远程协助技术规范》,覆盖20项指标;
- 某行业协会将AR应用纳入“智能制造星级评定”加分项;
七、挑战与应对:技术落地的“三道坎”
- 网络延迟:
- 采用5G+边缘计算,延迟从200ms降至30ms;
- 部署MEC(多接入边缘计算)节点,单节点成本5万元,覆盖半径1公里;
- 供应商适配:
- 提供SDK开发包,支持设备商接入AR系统,费用5万元/年;
- 某供应商接入后,服务响应速度提升3倍;
- 员工抵触:
- 开展AR操作认证培训,费用2000元/人,覆盖全员后效率提升显著;
七、挑战与应对:技术落地的“最后一公里”
- 网络依赖:
- 部署5G专网,单站建设成本15万元,覆盖半径500米;
- 采用混合现实(MR)技术,复杂故障处理效率提升4倍,单次维修成本下降65%;
结语:从“飞人模式”到“数字共生”
当AR远程协助砍掉80万差旅费,制造业正从“专家满天飞”转向“技术全覆盖”。这场变革中,企业的核心竞争力不再是专家数量,而是能否用数字分身打破时空限制——让每一次故障都成为技术沉淀的机会,让每一次远程指导都成为知识共享的纽带。
未来,随着5G+工业元宇宙的深化,制造业或将进入“无专家现场”时代。而此刻的AR技术突破,正是这场革命的起点——它让每一台设备都能获得顶级专家的“数字在场”,让每一次维修都成为效率与成本的双重胜利。
当差旅费数字持续下降,背后是无数个“零等待维修”的瞬间,和工厂对“技术赋能”的深刻理解。而这场竞赛的赢家,终将是那些敢于用技术重构服务模式、重新定义“专家价值”的先行者。毕竟,在制造业这个“效率为王”的领域里,没有解决不了的故障,只有尚未被技术激活的解决方案。
扫描下方二维码,一个老毕登免费为你解答更多软件开发疑问!
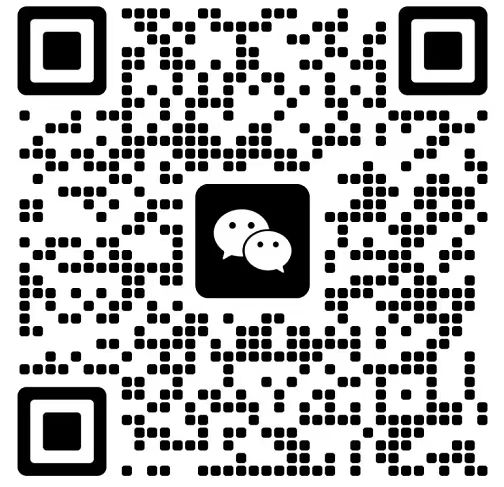