MRP,即物料需求计划(Material Requirement Planning),是一种在制造业中广泛应用的库存和生产管理方法。以下将详细解释MRP的概念、原理、作用,并通过一个实例来进一步说明其在实际应用中的运作方式。
一、MRP的定义与原理
MRP是一种基于产品结构和库存状况,通过计算机计算所需物料的需求量和需求时间,从而确定材料的加工进度和订货日程的计划方法。其基本原理是根据产品结构各层次物品的从属和数量关系,以每个物品为计划对象,以完工时期为时间基准倒排计划,按提前期长短区别各个物品下达计划时间的先后顺序。
在MRP中,需求被分为独立需求和相关需求两种类型。独立需求是指需求量和需用时间由市场或客户来决定的外部需求,如客户订购的产品;而相关需求则是指根据物料之间的结构组成关系由独立需求所产生的需求,如半成品、零部件、原材料等。
MRP的基本任务包括:从最终产品的生产计划(独立需求)导出相关物料(原材料)的需求量和需求时间;根据物料的需求时间和生产(订货)周期来确定其开始生产(订货)的时间。
二、MRP的作用
MRP在制造业中发挥着重要作用,主要体现在以下几个方面:
- 优化库存管理:MRP可以帮助企业维持合理的库存水平,避免库存积压或缺货现象的发生。通过精确计算物料需求量和需求时间,企业可以按需采购和生产,从而降低库存成本。
- 提高生产效率:MRP可以根据生产计划合理安排生产活动,确保生产过程的连续性和稳定性。同时,MRP还可以帮助企业及时发现和解决生产过程中的瓶颈问题,提高生产效率。
- 降低成本:通过优化采购和生产计划,MRP可以降低企业的采购成本和生产成本。此外,MRP还可以帮助企业减少库存积压和废品率,进一步降低成本。
三、MRP的实例讲解
以一家汽车制造商为例,该制造商生产多种型号的汽车,每种汽车由多种零部件组成。为了优化生产计划和库存管理,该制造商采用了MRP系统。
首先,根据市场需求和客户订单,该制造商制定了主生产计划(MPS),明确了各种型号汽车的生产数量和交货时间。然后,MRP系统根据产品结构(即BOM)和库存信息,计算出了各种零部件的需求量和需求时间。
在计算过程中,MRP系统考虑了零部件的提前期(即采购或生产所需的时间)、库存量和安全库存等因素。通过计算,MRP系统得出了建议的采购计划和生产计划。
根据MRP系统的建议,该制造商及时采购了所需的零部件,并合理安排了生产活动。同时,MRP系统还实时监控了库存水平和生产进度,确保了生产过程的连续性和稳定性。
通过采用MRP系统,该汽车制造商成功优化了生产计划和库存管理,提高了生产效率和产品质量,降低了成本和库存积压。此外,MRP系统还为企业提供了实时的库存和生产信息,帮助企业更好地应对市场变化和客户需求。
综上所述,MRP是一种重要的库存和生产管理方法,在制造业中发挥着重要作用。通过优化生产计划和库存管理,MRP可以帮助企业提高生产效率、降低成本、提高产品质量和市场竞争力。
扫描下方二维码,一个老毕登免费为你解答更多软件开发疑问!
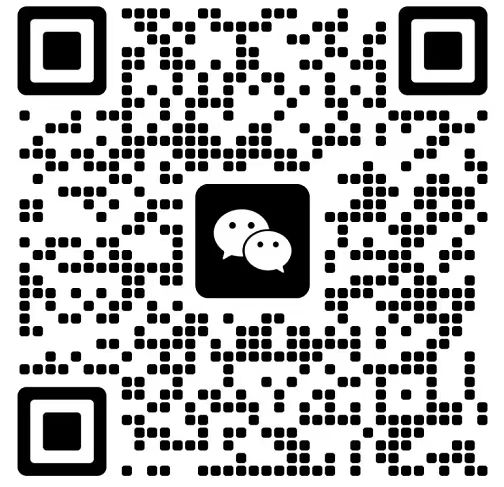